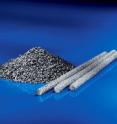
The new solution is simpler: a composite material. The different materials are not merely slotted together or bonded, but mixed in a special process to form a single material. This process produces a homogeneous and fine-meshed electrically conductive network. The composite possesses the desired chemical stability and low weight, coupled with the electrical and thermal conductivity of metals. As it will no longer be necessary in future to integrate metal circuit boards and the components will soon be able to be produced in a single work step, the production costs and the weight of the material are drastically reduced.
Automobile and aircraft manufacturers, in particular, will benefit from this development. The headlamp housings on a car, for example, are made of plastic. Until now, punched metal sheets have been installed in order to illuminate the headlamps. If the housings were fitted with circuit boards made of the conductive plastic-metal hybrids, they could be produced more efficiently and at lower cost than ever before. Many components of an aircraft, such as the fuselage, are partly made of carbon fiber composites (CFC). However, they lack the ability to conduct electricity. A stroke of lightning would have fatal consequences. A plastic-metal hybrid would be a good alternative for discharge structures on components.
Source: Fraunhofer-Gesellschaft
No comments:
Post a Comment